
Precision in Motion
Industrial Surface Solutions
DYYRENT deburring systems deliver unmatched precision for critical surface finishing applications. With 15+ years of engineering expertise, our automated solutions serve aerospace, automotive, and medical industries. Our patented technology ensures consistent results for complex geometries, achieving Ra 0.1μm surface finishes while maintaining ±0.01mm dimensional accuracy. Discover how our ISO 9001-certified systems optimize production workflows across 9 essential surface treatment processes.
Advanced Deburring Systems for Modern Manufacturing
DYYRENT's CNC-controlled deburring machines combine German engineering precision with smart automation capabilities. Our patented adaptive pressure control system ensures consistent results across complex geometries, eliminating manual rework. The modular design allows configuration for both high-volume production lines and specialized low-volume applications.
Key Industries Served
Trusted by Tier 1 suppliers across critical sectors requiring micron-level precision:
- Aerospace: Turbine components, structural airframe parts
- Automotive: Transmission systems, EV battery enclosures
- Medical: Surgical instruments, implant surfaces
- Electronics: 5G antenna components, semiconductor parts
Technical Specifications Overview
DYYRENT Solutions: Precision for Flat Metal Surfaces
Serving Global Manufacturing Leaders Across Key Sectors
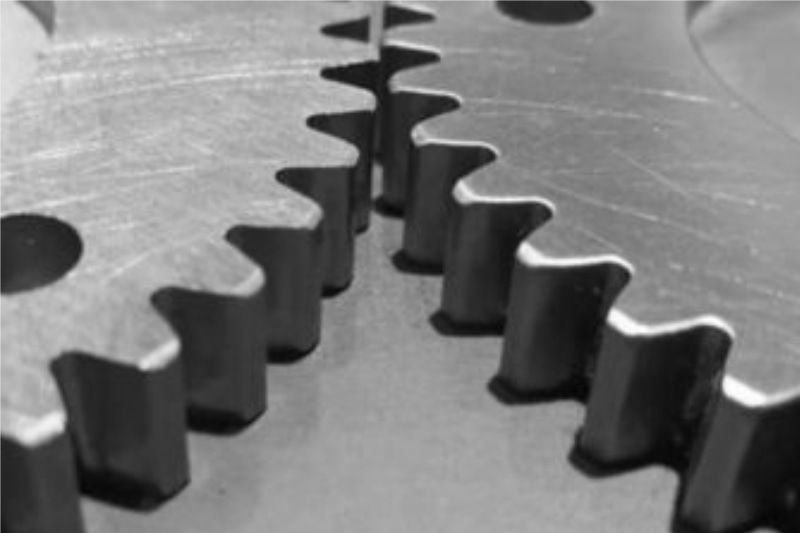
Aerospace Components
Precision finishing for turbine blades and structural elements
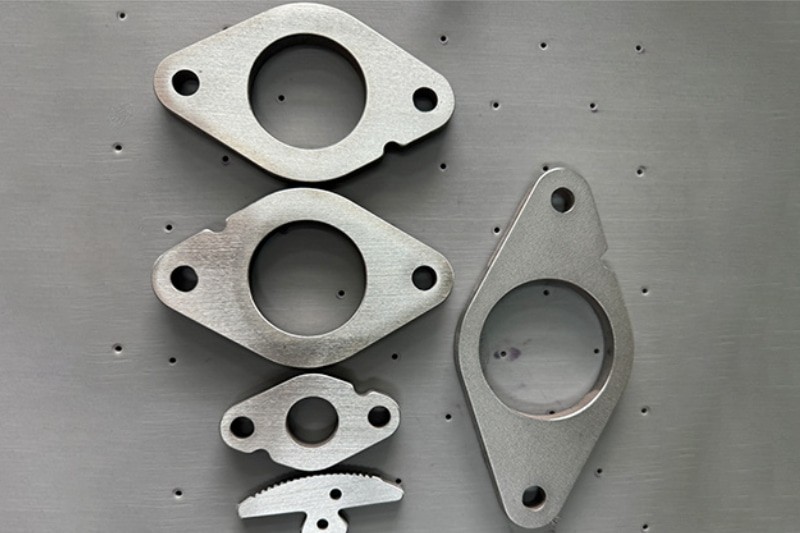
Automotive Systems
High-volume processing for transmission and EV components
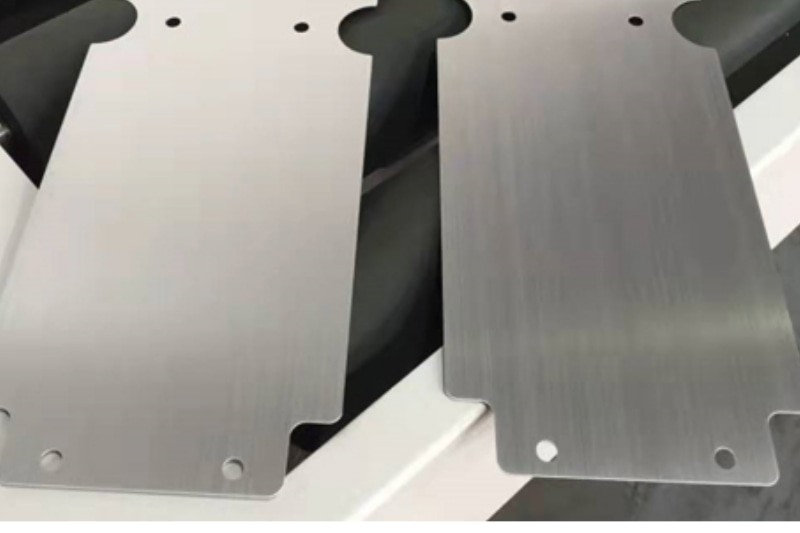
Medical Devices
Micro-deburring for surgical instruments and implants
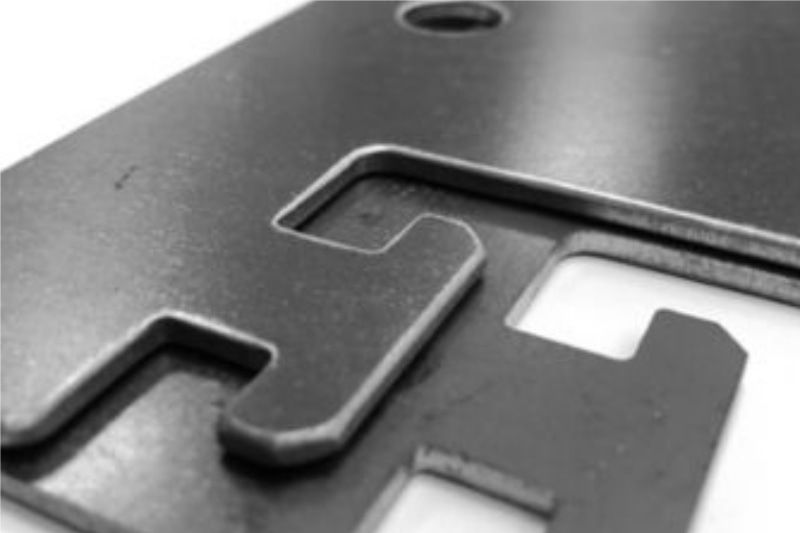
Energy Systems
Surface treatment for turbine components and heat exchangers
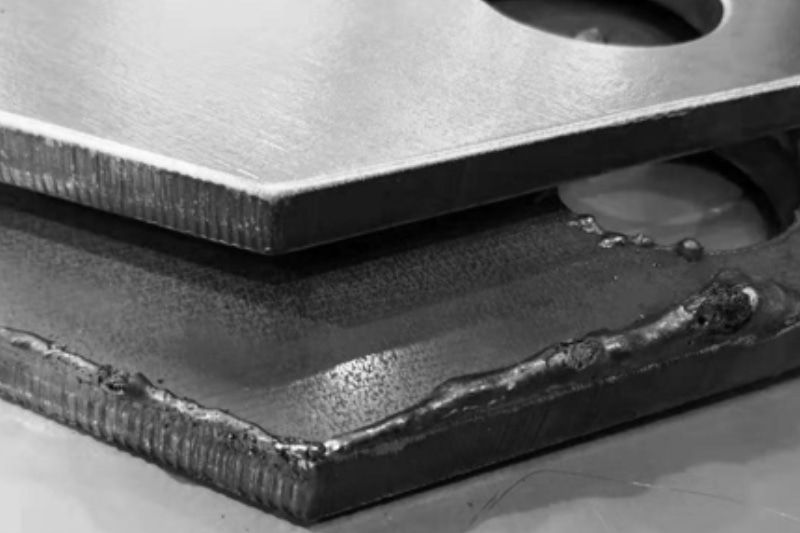
Advanced Electronics
Delicate finishing for semiconductor and 5G components
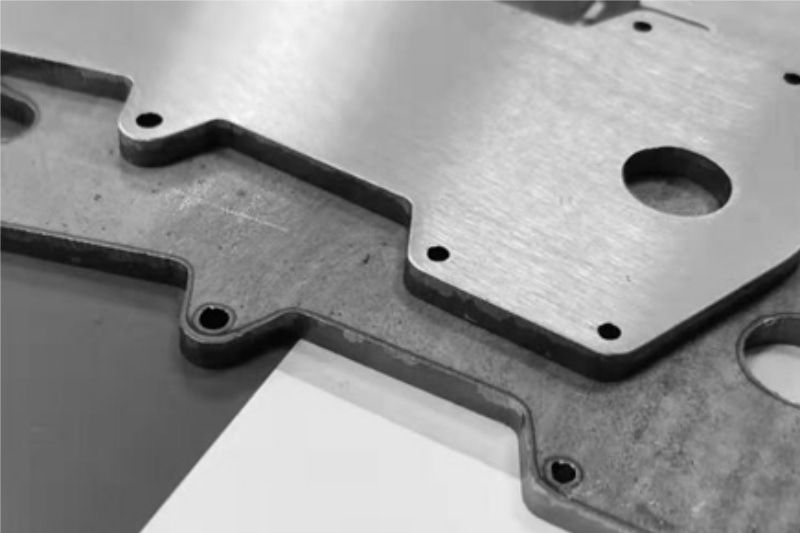
Defense Contracting
Secure processing for mission-critical hardware
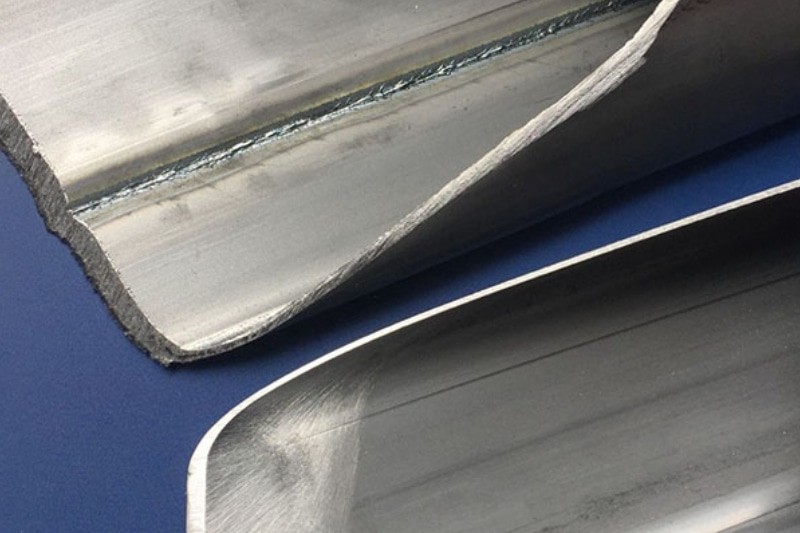
Marine Engineering
Corrosion-resistant surface treatments
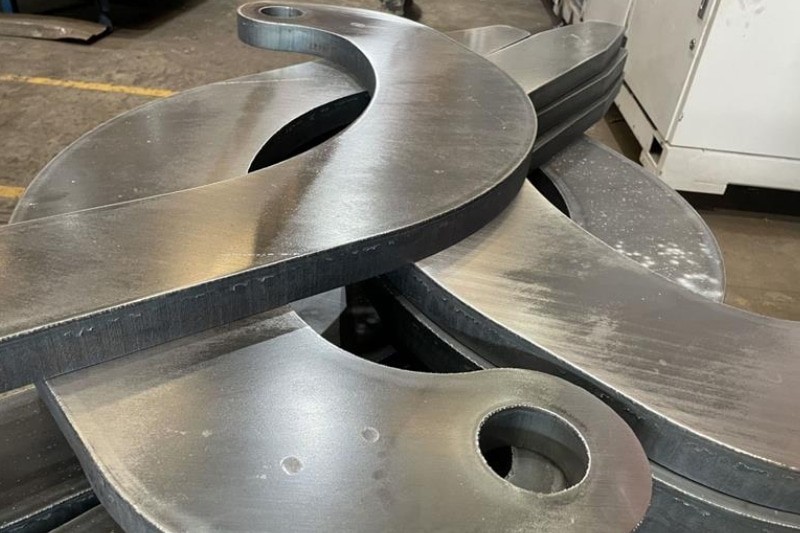
Industrial Machinery
High-precision finishing for hydraulic components
Precision Deburring Workflow
8-Step Automated Quality Assurance Process
Material Loading
Automated conveyor system with precision fixturing
Laser Alignment
3D scanning for part positioning (±0.01mm)
Adaptive Deburring
Multi-axis CNC machining with real-time pressure control
Quality Inspection
Automated vision system with micron-level accuracy
Surface Finishing
Automated polishing to achieve Ra 0.1μm finish
Part Unloading
Robotic arm handling with anti-scratch protection
Data Reporting
Real-time production analytics & quality documentation
Preventive Maintenance
Automated tool wear monitoring & alerts
Why Choose DYYRENT
Engineering Excellence in Deburring Technology
Micro-Precision Machining
Achieve ±0.005mm tolerance control with our patented multi-axis CNC system
High-Speed Processing
85% faster cycle times compared to manual deburring methods
Military-Grade Durability
40% longer service life with aerospace-grade components
Smart Automation
AI-powered adaptive pressure control system
Energy Efficient
30% lower power consumption than industry average
Global Support
24/7 technical support with 4-hour response guarantee
DYYRENT · Client Testimonials
Trusted by manufacturers in 120 countries worldwide
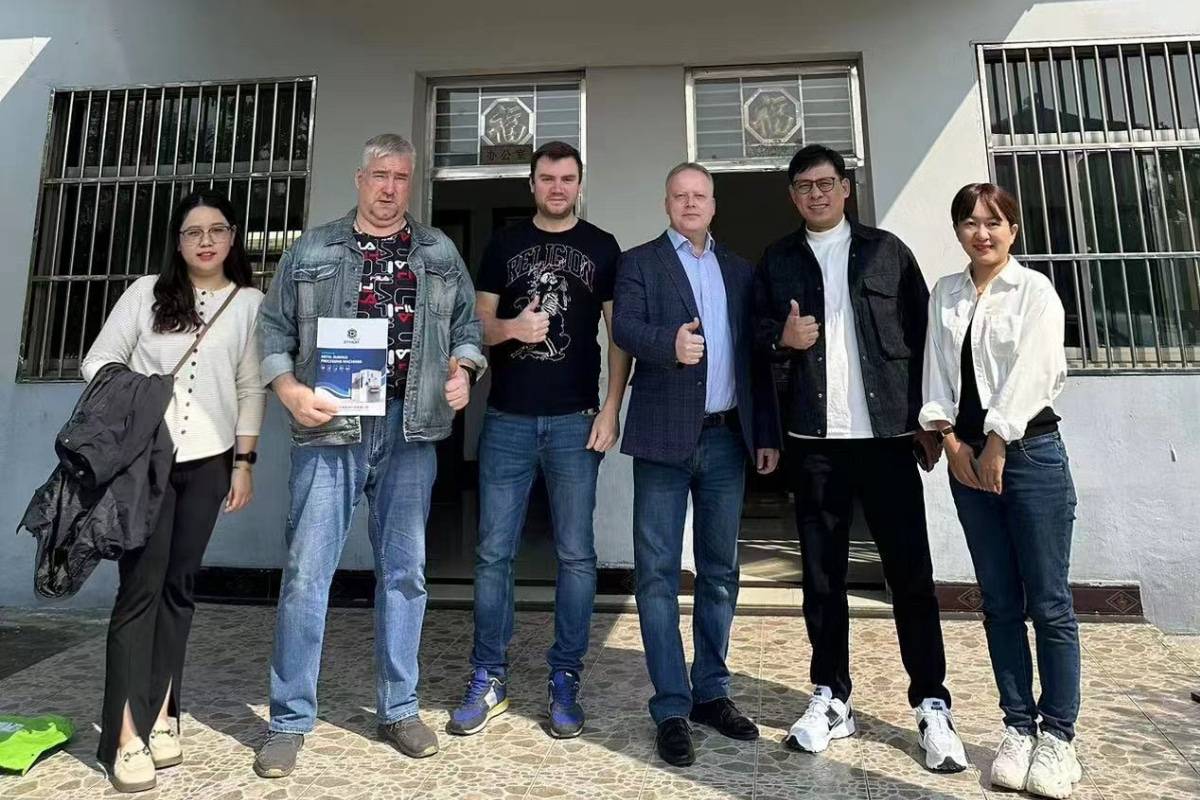
Precision Auto Components
"The automated deburring system reduced our post-processing time by 40% while maintaining ±0.02mm consistency."
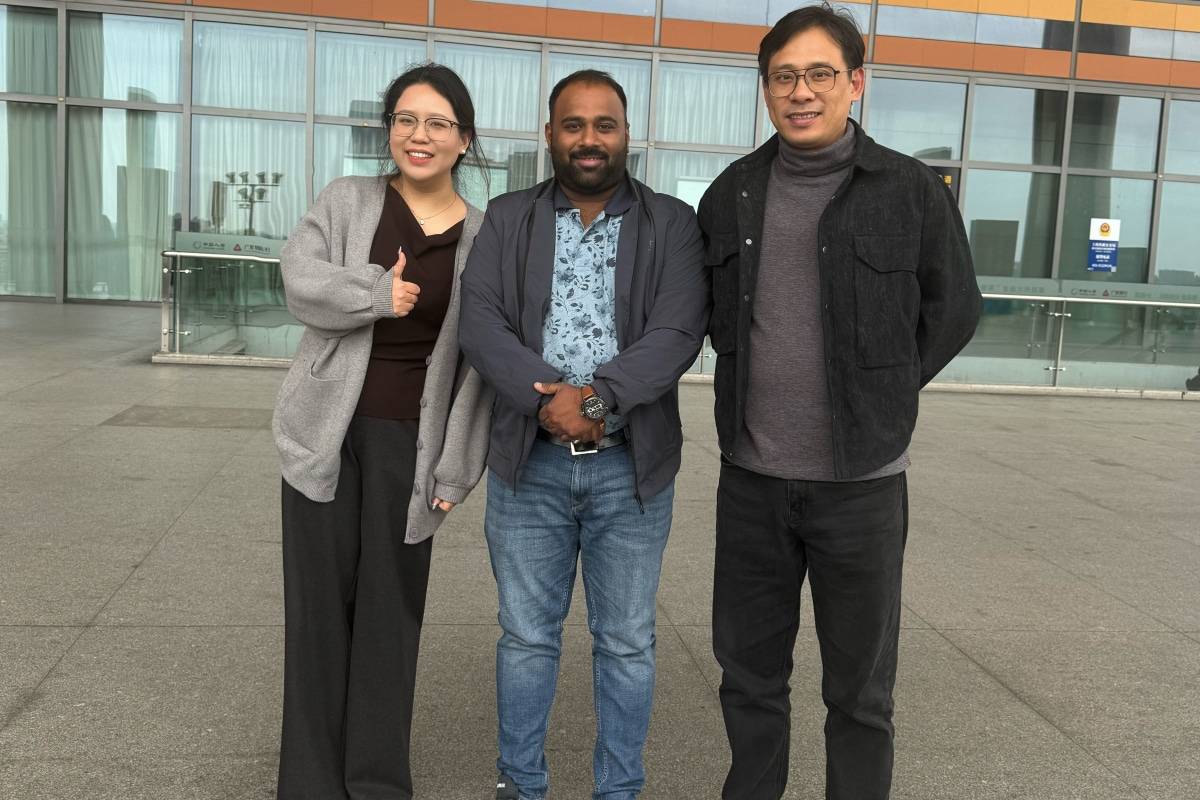
Precision Auto Components
"The automated deburring system reduced our post-processing time by 40% while maintaining ±0.02mm consistency."
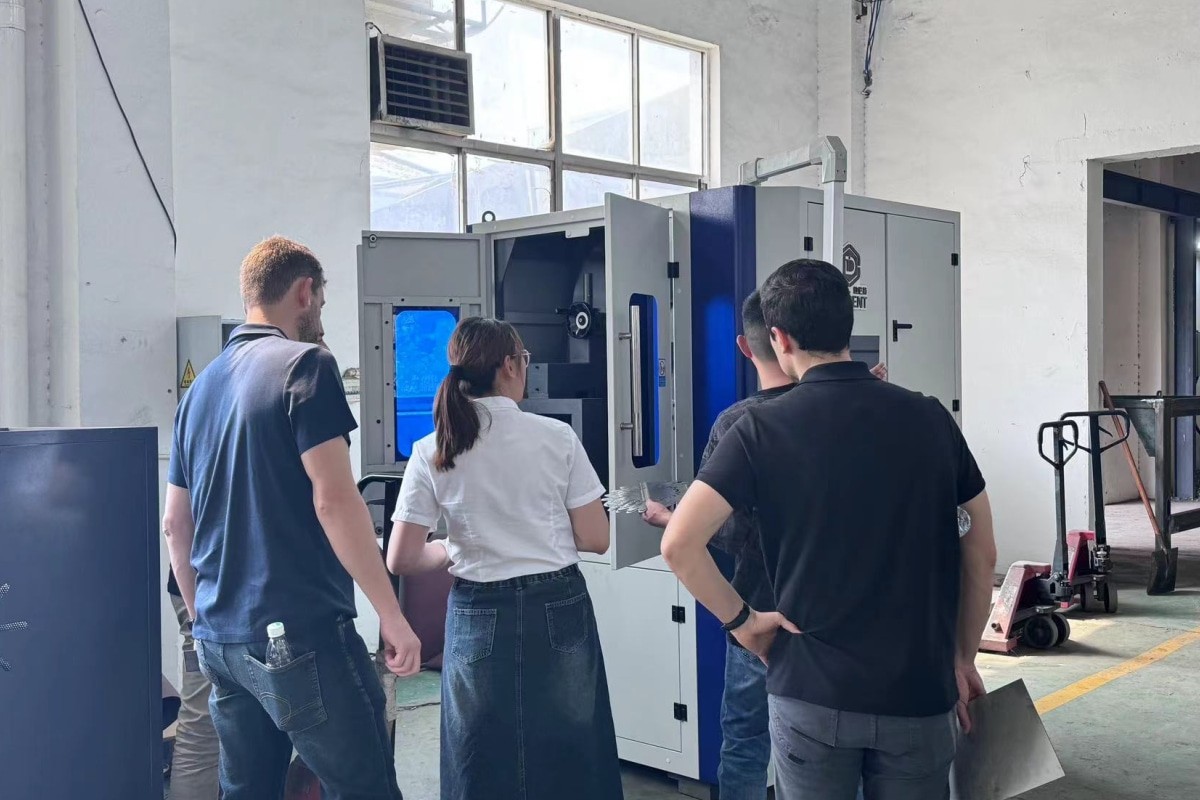
Precision Auto Components
"The automated deburring system reduced our post-processing time by 40% while maintaining ±0.02mm consistency."
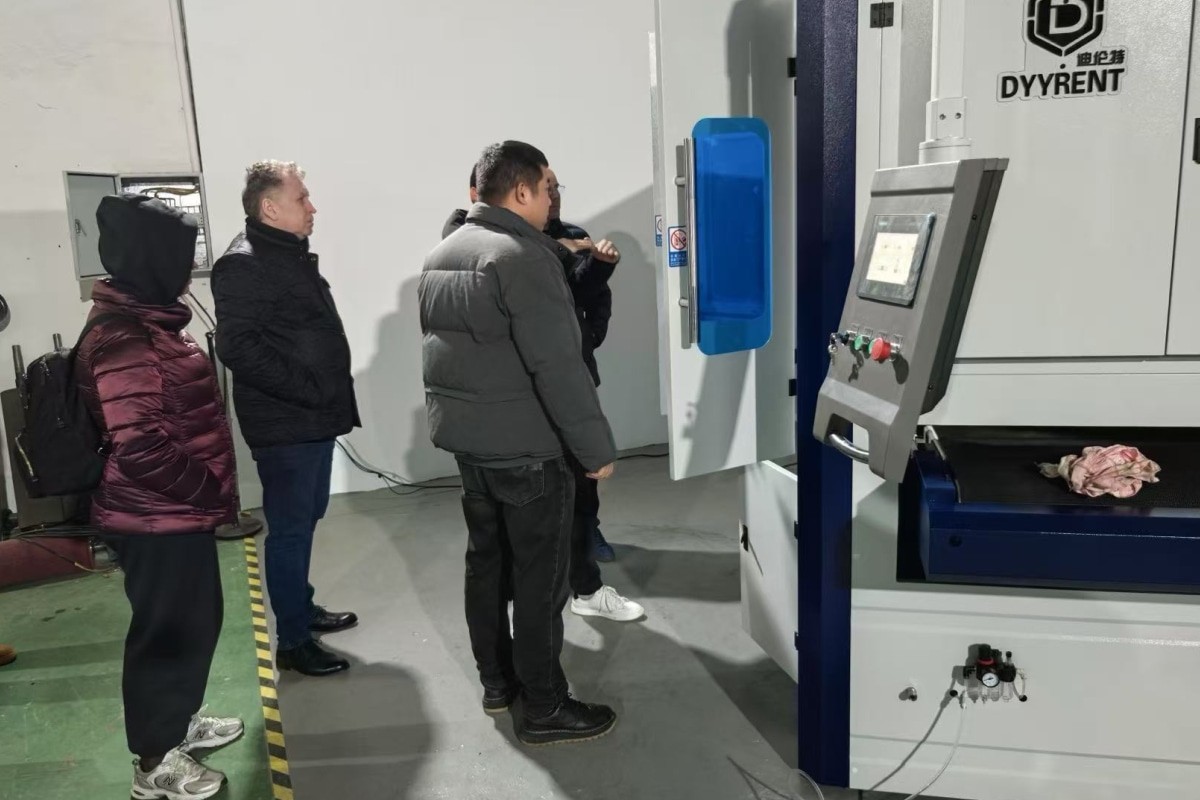
Precision Auto Components
"The automated deburring system reduced our post-processing time by 40% while maintaining ±0.02mm consistency."
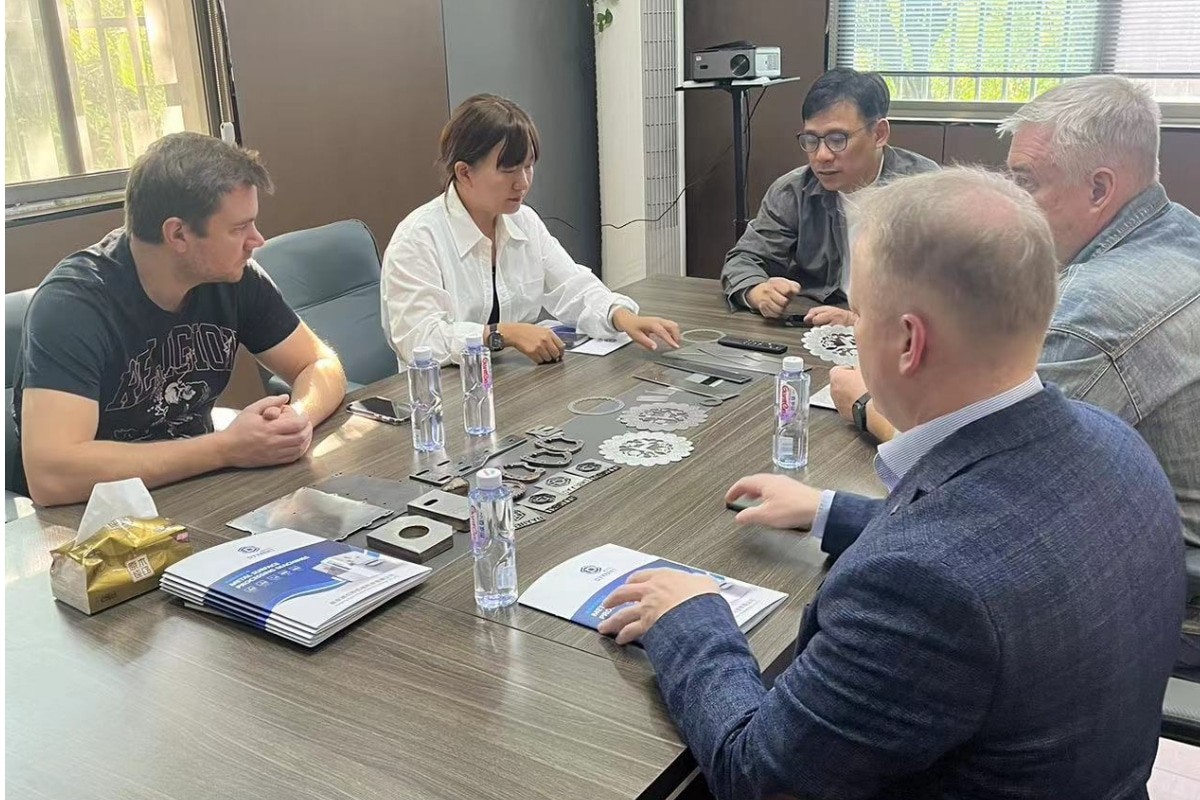
Precision Auto Components
"The automated deburring system reduced our post-processing time by 40% while maintaining ±0.02mm consistency."
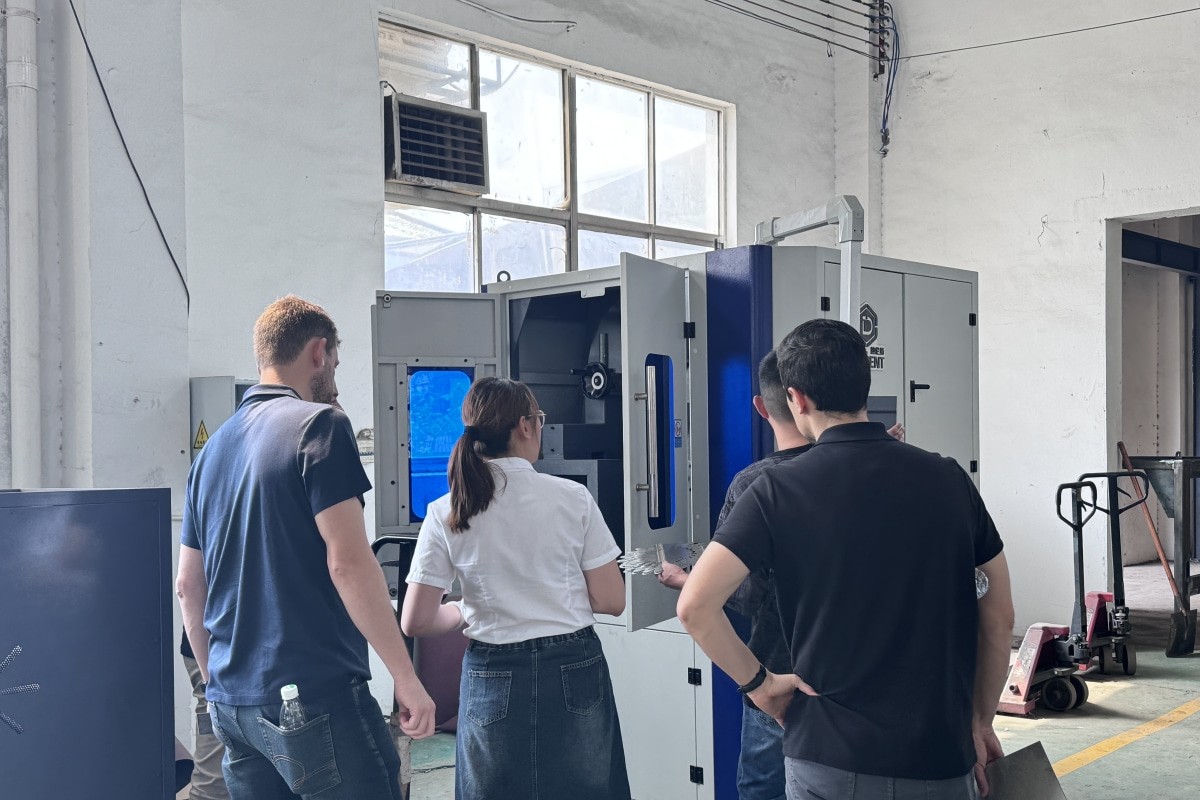
Precision Auto Components
"The automated deburring system reduced our post-processing time by 40% while maintaining ±0.02mm consistency."
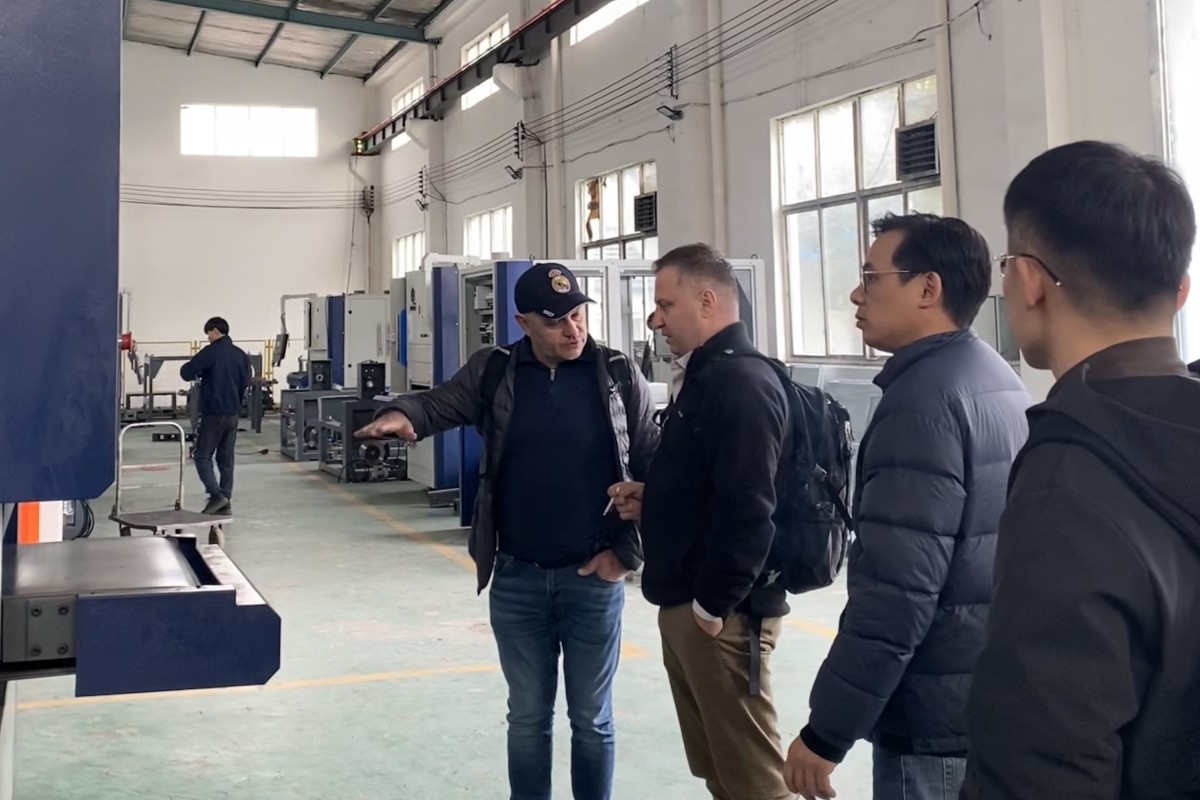
Precision Auto Components
"The automated deburring system reduced our post-processing time by 40% while maintaining ±0.02mm consistency."
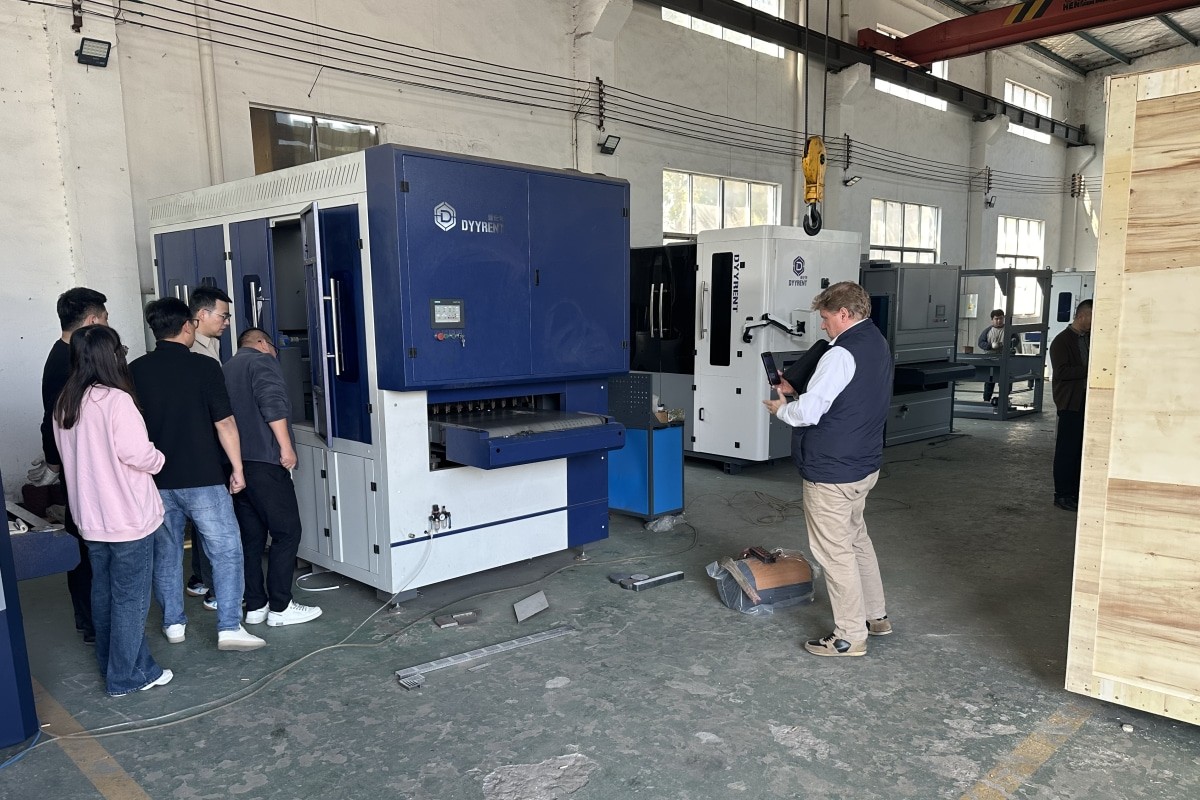
Precision Auto Components
"The automated deburring system reduced our post-processing time by 40% while maintaining ±0.02mm consistency."

Precision Auto Components
"The automated deburring system reduced our post-processing time by 40% while maintaining ±0.02mm consistency."